|
|
 |
Ceramic
Injection Molding |
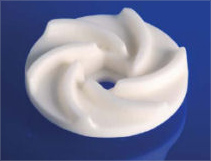 For components requiring high precision and medium to high volumes Stourport offers Ceramic Injection Moulding (CIM). CIM is an innovative forming technique to manufacture a range of components, including those with a high geometric complexity, offering an economic solution for difficult production problems. The CIM process begins with very fine ceramic powders. Using sophisticated mixing technology the powders are compounded with thermoplastic binders to produce a homogeneous pelletised feedstock. The binders form a liquid medium which carries the ceramic powders into the mould during the injection stage. Using an injection moulding machine similar to that used in conventional plastic moulding, the molten feedstock is forced into a mould cavity forming a net shape part. Moulds can be single or multi-cavity configurations. After forming the part it then goes through two thermal processes. First is pyrolysis to remove the binder, followed by sintering in a high temperature kiln to form a fully dense ceramic component. During sintering the component shrinks uniformly by as much as 20% while retaining the complex shape. With good process control close tolerances can be obtained, therefore machining of the part after sintering is usually not necessary. |
|
The benefits of Ceramic Injection Moulding |
- Provides unique, economic solutions to increasingly stringent material and product design requirements
- Excellent batch to batch repeatability and process capabilities achieving a tolerance of +/– <0.3%
- High surface finish quality without the need for additional finishing processes
- Accommodates extremely complex geometric components
- Superior material performance, high hardness and mechanical strength, wear, corrosion and weathering resistant, dimensionally stable, high working temperature and good electrical insulator
- Also used for metallised applications
|
|
Ceramic Vacuum Molding |
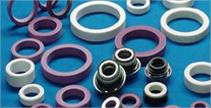 Moulding is becoming a powerful technique for the fabrication of structured ceramic microcomponents. The aspect ratio of the structures to be produced has always been a limiting factor for the applicability of moulding techniques. A vacuum moulding process was developed to supply high aspect ratio ceramic structures. Special designed paraffin wax feedstocks based on alumina and sodium chloride moulds were used for the patterning of periodic columnar structures of some centimeter extension with columns of some millimeter height and an aspect ratio of more than 11. It is shown that the processing technique described features a route to obtain ceramic structures of high precision with a minimum of technical requirements. |
|
|
 |
|
|